Custom Plastic Injection Moulding
How Does Plastic Injection Moulding Work?
The process of manufacturing moulded parts is intricate. Before moulding even begins, we provide comprehensive manufacturability feedback and consultative design services to help you avoid common mould design issues. Our production process is thoroughly documented and optimized using scientific moulding techniques, ensuring you receive high-quality parts consistently with every production run.
Critical-to-quality (CTQ) dimensions specified in your models guide us in identifying the most important areas for the success of your parts. Once moulding begins, the process and samples are qualified using automated inline CMM technology, generating a detailed First Article Inspection (FAI) and process capability study without additional lead time.
Our thermoplastic injection moulding process typically involves an aluminium mould without heating or cooling lines, resulting in slightly longer cycle times. As part of the scientific moulding approach, our moulders independently optimize and monitor fill speed, hold pressure, and hold time, while periodically inspecting part quality and appearance. During moulding, an automated inline CMM ensures dimensional accuracy and generates a detailed process capability study and FAI report.
Resin pellets are loaded into a barrel, where they are melted, compressed, and injected into the mould’s runner system. The hot resin is injected into the mould cavity through the gates, and the part is formed. Ejector pins then remove the part from the mould, and it falls into a loading bin. Once the run is complete, parts (or the initial sample run) are packaged and shipped shortly thereafter.
Our Plastic Moulding Capabilities
Our fundamental guidelines for plastic injection molding cover key design considerations aimed at improving part moldability, enhancing cosmetic appearance, and reducing overall production time.
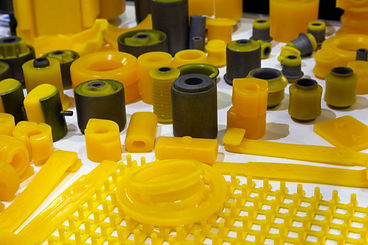
Materials
We offer a wide range of over 100 thermoplastic and thermoset materials. If you're seeking alternative material options, be sure to explore our guide to resin substitutes for ABS, PC, PP, and other commonly molded plastics.

Finishing
Draft angle requirements will depend on the desired finish. Industry-standard Mold-Tech finishes are also offered.

